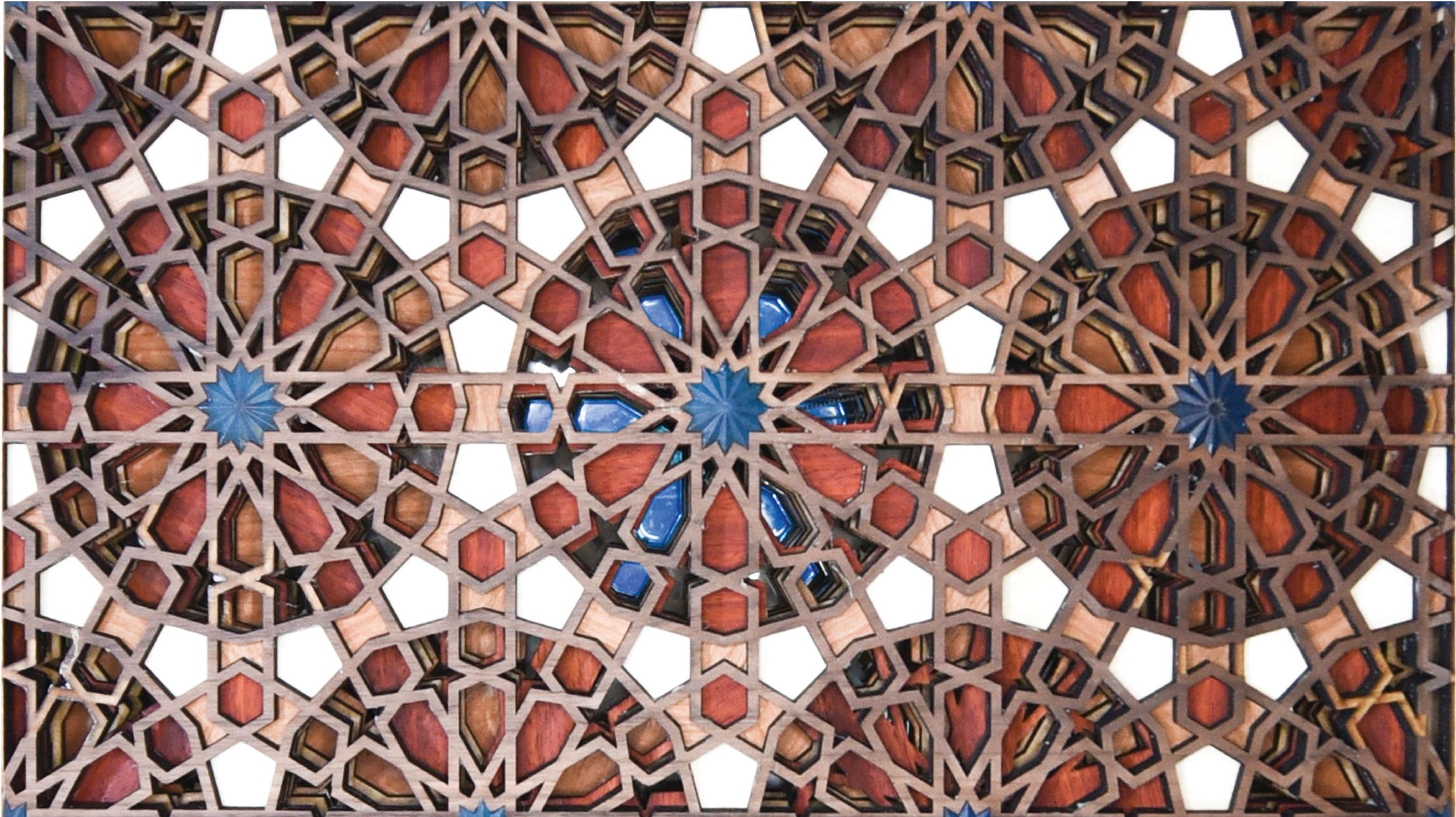
Mashrabiya: Kinetic facade system
Fab Academy 2021 - Final project
Mashrabiya:
Kinetic facade system
Fab Academy 2021 - Final project
Team: Independent. Year: 2021
Location: Amman, Jordan Phase: Product prototype.
Introduction
Fab Academy is a 20 weeks program where you learn new technology related to digital fabrication each week. This part of my portfolio demonstrates my experimental trials of bridging the gap between culture and digital technologies. Mashrabiya was the final project for this diploma that I worked on in parallel with the weekly assignments for five months. The main objective of these projects was to show the compatibility between old Arabic crafts and digital fabrication, which helped integrate these products into the community’s daily life. They also ease introducing new technologies to the younger generation of students through projects related to their culture.
Background
Mashrabiya is originally an element of Arabic architecture. It is a projecting oriel window enclosed with carved wood latticework located on the upper floors, sometimes enhanced with stained glass. It is traditionally used to catch and passively cool the wind; jars and basins of water were placed to cause evaporative cooling. The original Mashrabiya works using passive air pressure coming from the courtyard, so if you want to add it to an apartment, you need to modernize it. I tried to do that, keeping some authenticity to the product hiding all the mechanical parts, and using Arabic wood technics.
Project brief
Mashrabiya is a lighting and ventilation unit inspired by arabesque mosaic; it provides multiple options considering light, patterns, and ventilation. Mashrabiya is made using natural wood, epoxy, and mechanical parts. It was made of various geometrical layers that move in angular combinations to create different iterations. It is assembled using interlocking and press-fit techniques. It is wirelessly and manually controlled or via a mobile application. The mechanical movement combines the gear systems and timing belts that work responsively to heat and light sensors.
Project process
During this phase, an analysis of the original model was conducted, encompassing the entire process, including floor plan design. Subsequently, decisions were made regarding necessary modifications and the level of sophistication required for the mechanical components. This step played a crucial role in achieving an optimal balance between a passive and active system.
The early prototyping phase involved conducting testing trials with inexpensive materials to validate the proof of concept. This informed the selection of the desired pattern and workflow for the entire project, along with the identification of potential challenges.
In this stage, a comprehensive 3D model for the machine was developed, incorporating movement and assembly simulations using software such as Solidworks. Based on these simulations, the appropriate fabrication technology for each part was chosen, and files for fabrication were meticulously prepared.
Project process
In this stage, worked with multiple types of wood to create an arabesque mosaic piece. The use of natural materials like rosewood, maple, cherry, and walnut wood in this project helped maintain the product's authenticity. Press-fit old techniques were employed in the project assembly.
Utilized laser cutting technology to craft complex geometrical patterns and other machine components. Various processes, including cutting wood veneer for pattern formation and etching identical geometrical designs on acrylic to enhance light visibility.
Employed casting and molding to produce geometrical 3D shapes as central pieces of the pattern. Oomoo silicone was used for the mold, and various epoxy shades were cast into acrylic pieces to create stained mosaic glass.
Utilized 3D printing to create molds for casting and custom-made mechanical parts using an SLA printer. The mechanical components facilitated the transfer of movement from the motor to the panels through a timing belt.
Operated panels using six servo motors that generated synchronized angular combinations. Addressable LED lights were employed for light patterns, and output parts were dependent on signals received via HC-05 Bluetooth or manual inputs. Pressing a button multiple times allowed changing iterations.
Operated panels using six servo motors that generated synchronized angular combinations. Addressable LED lights were employed for light patterns, and output parts were dependent on signals received via HC-05 Bluetooth or manual inputs. Pressing a button multiple times allowed changing iterations.
Completed early prototyping with Arduino, designed the PCB board using Eagle, and produced it using a CNC milling machine. The PCB board was programmed using the C language, serving as a permanent controller for the machine.
The images above depict the outcome of rotating one layer of wood by 30 degrees, unveiling the acrylic layer beneath. It's essentially a play of revealing and concealing.
The images above showcase various light iterations. While all mechanical pieces are precisely adjusted and secured based on their size and location, the light can extend beyond the facade system by adjusting its intensity, color and movement.